By using modular and off-site construction solutions, Transport for London and partners are now set to revolutionise upgrades and repairs to essential track-side installations.
Tfl faced an infrastructure restoration problem. A track-side building housing an electrical switch-box near the Willesden Depot in West London had fallen into disrepair and needed urgent attention.
Water had found its way into the building, and was seriously threatening catastrophic failure of vital electrical equipment inside.
The two traditional solutions were both problematic.
Removal and replacement of the building would require planning approvals, delays and high costs.
But, track-side repair of the facility would involve danger from the proximity to live rails, along with likely disruption of rail services.
Live rails are a feature of London Transport infrastructure that complicates track-side maintenance and construction, since safety concerns often require power shut-off. So this solution would also incur high costs.
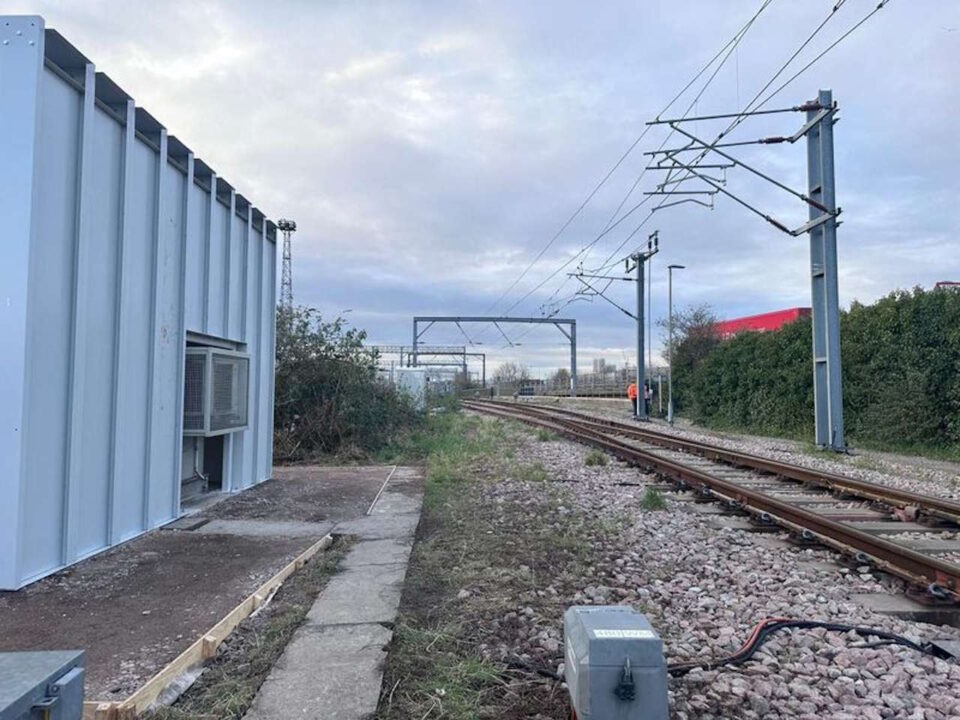
So, Tfl turned to UB Infrastructure, specialists in rapidly assembled low cost structures, for a safe, quick and cost-effective solution.
Their solution was to use a modular shell of non-corrosive aluminium to cover and waterproof the existing facility. Advantages of this approach were that minimum on-site work was required, the costs were significantly lower, and the expected lifespan of the structure would be longer.
UB Infrastructure then turned to Leicester firm ADS Laser cutting to prefabricate the shell components off-site.
ADS produced a kit of laser-cut aluminium panels that were folded and packaged off-site. Their low-weight reduced transportation costs, sped up on-site delivery and reduced assembly time to just two days.
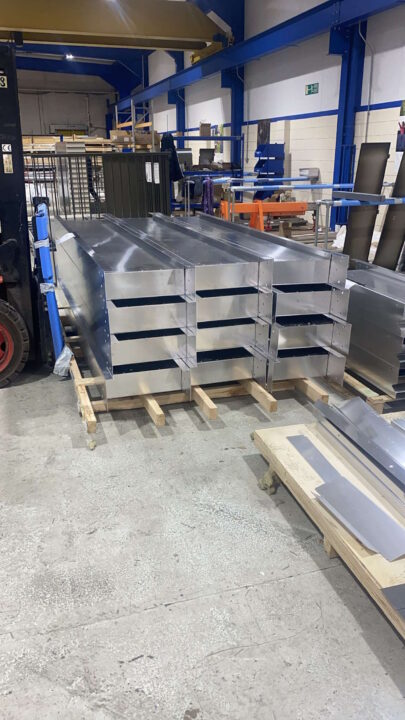
Installation of the modular cladding system at Willesden was carried out by Walker Construction.
As an added bonus, this new solution is more environmentally friendly than previous methods, with the completed building projected to deliver a 97% energy efficiency saving.
The project was completed with very significant cost and time savings and has led to a modular solution that can be rolled out across the UK rail network, delivering longevity and sustainability to line side infrastructure.
Modular and off-site solutions within construction are growing at pace and it has been a privilege to partner with the UBI team to deliver what we believe is a game changer for UK rail infrastructure
Stuart Rowan, Production Director
Responses