The Holden F5 Locomotive Trust has issued a report on the work it carried out last year.
The Trust, formed in 2003, is building a replica of the Great Eastern Railway’s M15r (later known as LNER F5) Class of locomotives, which was designed by James Holden.
Wheelsets
The Trust has ordered all the materials needed for the wheelsets and 80% of the materials have arrived at Riley & Sons workshop in Heywood.
When the tyres arrive, the Trust can begin assembling firstly the leading and trailing wheelsets and then the driving wheels.
The Trust had hoped to have reached this stage sooner, but decided to prioritise getting the right materials from the right suppliers worldwide, which takes time. The Trust is confident that the engineered items will stand the test of time in the environment they have to work in.
Crank Axle
The Trust was using the J15 crank drawing as a baseline for the design for the axle. The original locomotives ran with one-piece forged crank axles, and although these can still be manufactured today, the Trust has decided that it prefers the built-up type.
Bob Meanley has drawn up the drawings needed for getting the individual part materials ordered for the axle component, crank pins and webs.
Radial Guides and Ancillary Parts
The Trust obtained costings for main castings in September, but these were very expensive, so the Trust is taking an alternative approach.
Elliot Powick has been redesigning the casting to a hybrid casting/fabrication design. There will be one small pattern required for the axle box sections, which can then be used to cast four identical patterns. Basic machining will be added to the castings to allow the rolled centre sections to be added and the complete design welded.
Once this is completed, the welded assembly will have its finishing machining added and ready for fitting. The radial guides are yet to be finished machined. There are only a few companies which can accommodate this task. The supplier that the Trust had chosen has stopped trading, so the search is on for a new machinist who can complete the job.
Hornblocks
The Trust has put out patterns for quotation and the castings should be underway in the first half of this year. Along with the front and rear radial guides, these are the last pieces of the fixed frame jigsaw. Once fitted, they will be ready to receive and fit the new wheelsets from Rileys.
Axleboxes
Although the front and rear wheelset axleboxes are built into the large castings, the main wheelsets require their own. The locomotive requires two driving and trailing axleboxes (the driven wheelset has a larger design to cope with the extra forces exerted).
The computer-aided design (CAD) work for this is about four-fifths completed. Once this is finished, the Trust will put the four bronze axlebox patterns and castings out for tender. Below shows the drawing for the larger axlebox required.
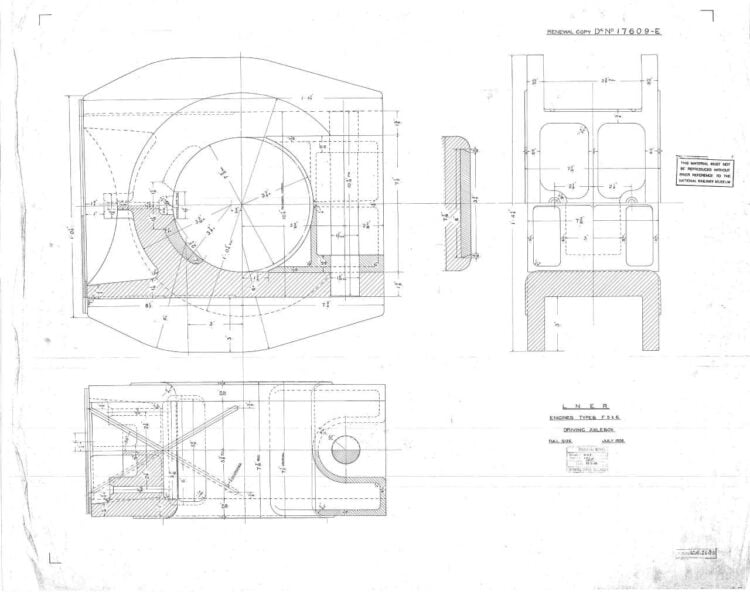
Springs & Spring Gear
TLW has been manufacturing the additional spring gear required to get the loco going. By the end of 2023, about 85% of the parts had been manufactured, and all hanging bracketry had been bolted/riveted to the frames.
The springs require specialist manufacture, so the Trust will be getting quotations from Owen Springs for all the main springs (seen below).
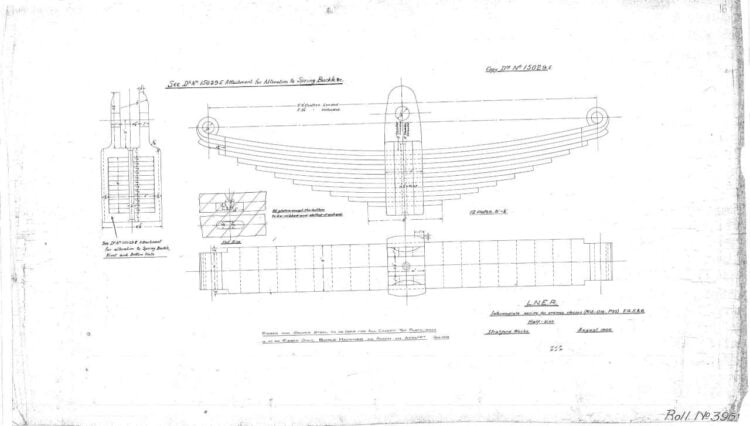
Together with the main wheel springs, the radial trucks require special side control springs manufactured for both front and rear trucks (shown below.)
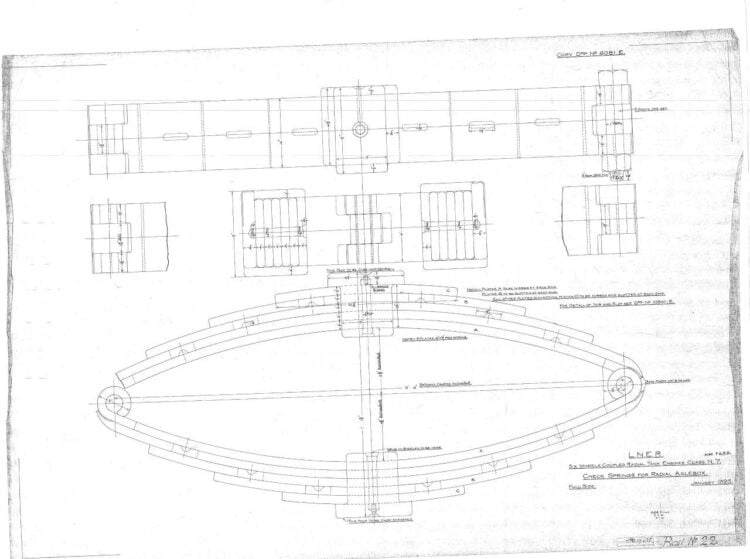
These along with the extra parts needed for the radial trucks and keeps will provide everything needed for when the wheelsets are ready to be fitted.
Pistons, Rods & Crossheads
TLW is drawing up a quotation for manufacturing the piston heads and rods. The CAD model for the crossheads is complete, and patterns and castings are being put out for quotation. TLW has received the front cylinder cover pattern, which will be cast at the same time as the crossheads.
The rear cylinder covers have been made and the glands are currently being manufactured. Once these are in place with the slide bars, the ‘motor’ side of the locomotive will be completed and fitted.
Elliot Powick signs off by admitting that 2023 has seen the degree of progress that he would have liked, attributing this to many factors, including his workload and personal life. Nevertheless, progress is being made and 2024 is looking more optimistic.
Responses
Great news, cannt wait to see this loco finished and running as its one of my favourites, love these little tank locos !