The Tyne & Wear Metro is preparing for its new fleet with the installation of precision technology that will transform how the trains will be prepped for service.
The installation of a new automatic wheel lathe marks a new and more efficient era for Metro, the labour-saving tool will provide a more streamlined approach to maintenance.
Swiss manufacturer Stadler is building the new fleet for Metro’s operator Nexus and has fitted the lathe at the purpose-built facility at Gosforth Metro depot which is currently undergoing a £70m rebuild.
The first of Metro’s new 46 trains will be arriving at the end of the year.
The wheel lathe can manage more precision repairs on trains’ worn wheels at just the touch of a button. An underfloor tool which is located in its own special train care unit machines the wheelsets as the trains simply drives over the top.
Michael Richardson, Head of Fleet and Depot Replacement at Nexus, said:
“The new wheel lathe is an exciting part of the Metro fleet replacement project. There is no doubt that it marks a new era for maintenance when it gets brought into use on the new Metro fleet.
“Stadler are making great progress with our new £70m depot and the investment in the most advanced maintenance technology is something we are all really looking forward to seeing.
“The new wheel lathe will transform how the wheels on the new trains are looked after. It will mean more effective and more efficient repairs, and all at the touch of a button.
“We’ll get to see this amazing piece of technology in action after the new train fleet has started to be delivered at the end of the year.”
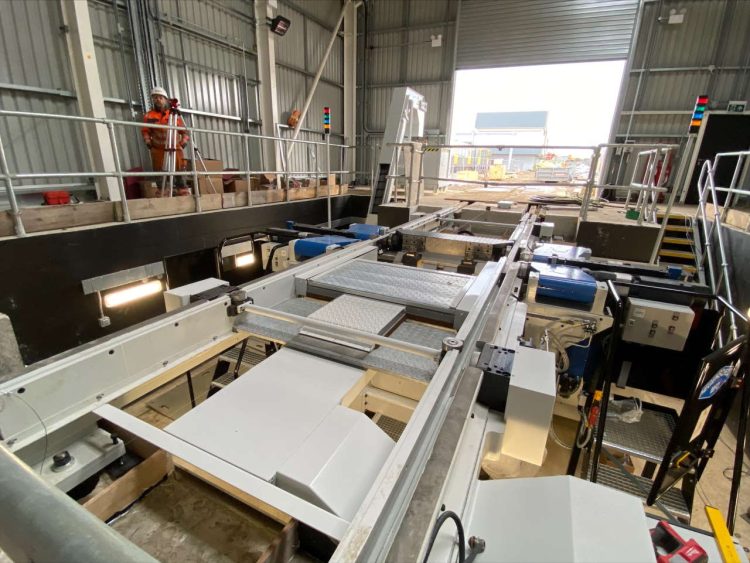
As trains carry out their daily operations, wear and tear creates what are known as flat spots on the wheels and is an issue that impacts trains throughout the world. A lathe re-profiles each wheel with pinpoint precision so that they are perfectly round once again which in turn brings a smoother ride for customers.
The current Metro depots lathe, which is set to be replaced soon, requires trains to be lifted to enable a wheel to be machined to remove the flat spots and is a more labour intensive process and less time-efficient to complete.
The new lathe which is built into the floor will remove this problem once the new fleet and depot are up and running and works by first measuring the size of each wheel before the amount of metal that requires cutting away is calculated and at this point, the machine moves onto the re-profiling of each wheel. The offcuts, which are called swarf, are recycled and once the cutting is complete, the lathe measures the wheels again to check them ahead of the train returning to service.
Paul Patrick, Engineering Director for Stadler Rail Service UK, said:
“The installation of this piece of equipment is another step in the process to build a new, state-of-the-art depot, which has been designed to ensure maximum availability and reliability of the fleet for decades to come. The new wheel lathe points to Stadler’s commitment to innovation and technology, with the ultimate goal of providing an excellent service for passengers.”
Responses